Five things this Bangladeshi factory does to prevent disaster
On the first round of sales visits, Motherhouse got orders for bags from 13 stores. It has expanded to create seven retail stores in China and Japan and pays its workers double the rate paid by other manufacturers. The leather factory is located in the now-infamous capital of Bangladesh, Dhaka proving that safety and success are not mutually exclusive.
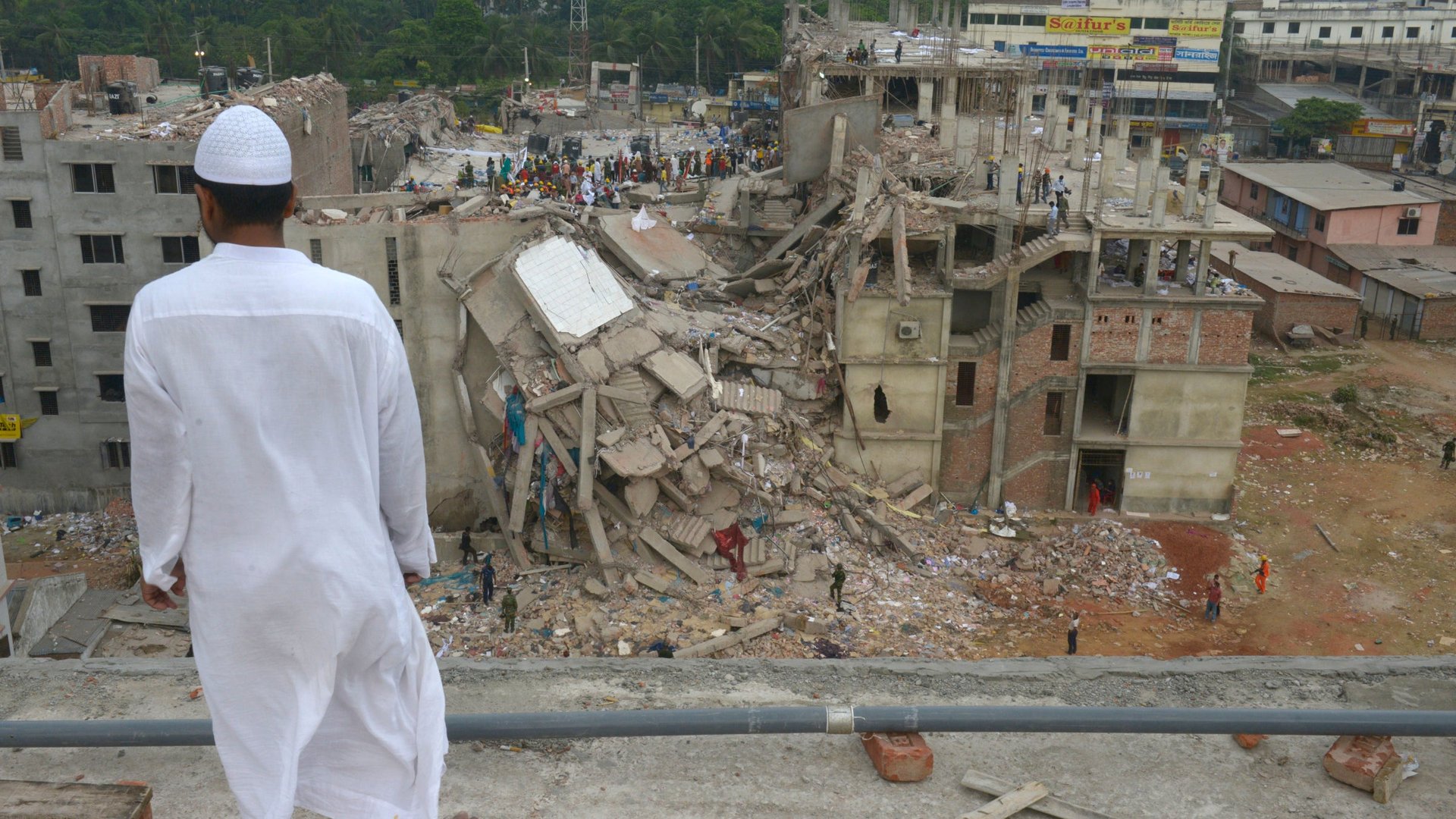
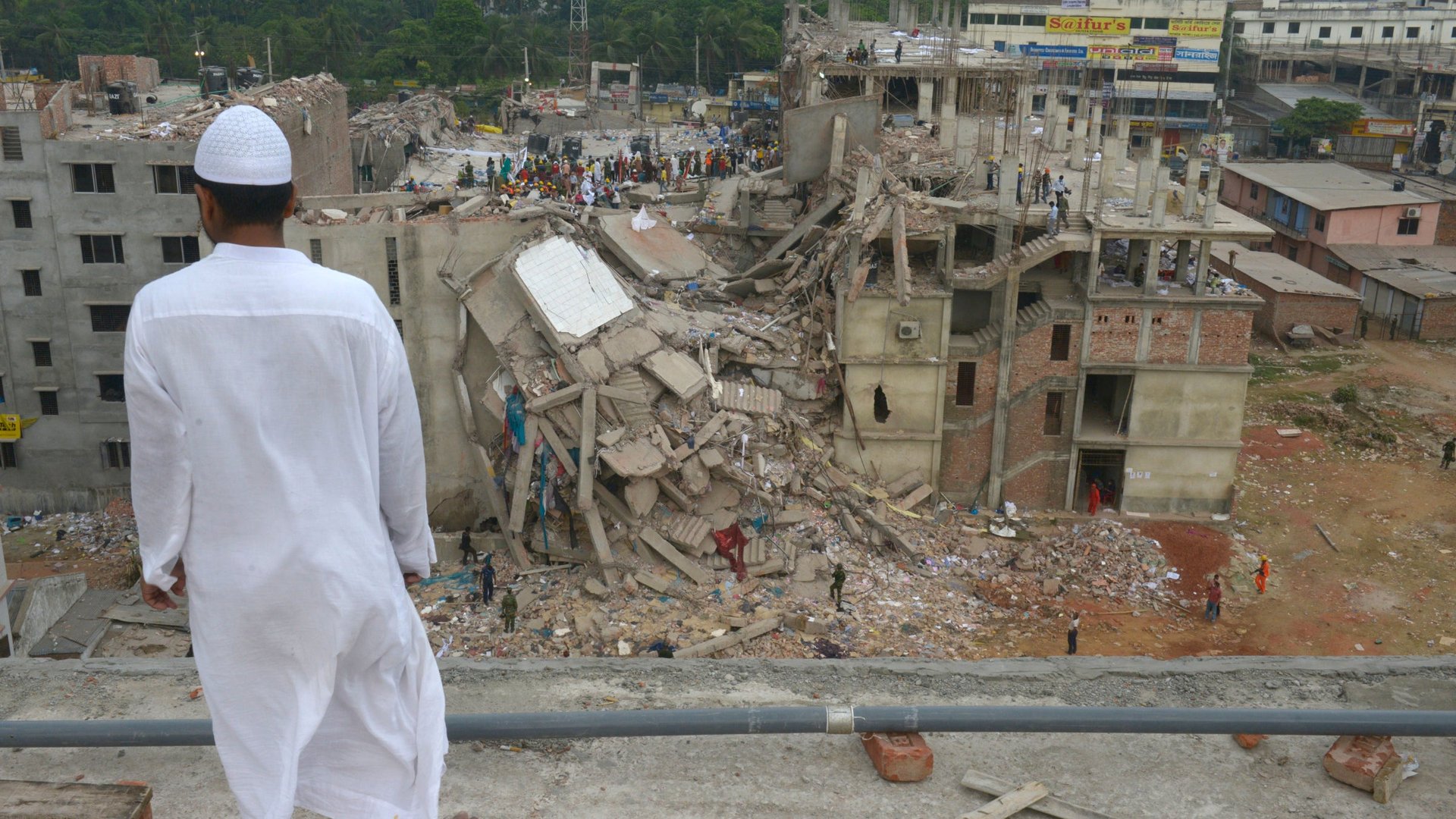
On the first round of sales visits, Motherhouse got orders for bags from 13 stores. It has expanded to create seven retail stores in China and Japan and pays its workers double the rate paid by other manufacturers. The leather factory is located in the now-infamous capital of Bangladesh, Dhaka proving that safety and success are not mutually exclusive.
“The quality of bags surprised people who think that when you get something from a poor country it’s going to be low quality and low price. We went for high quality at a middle price and it worked,” says founder and Tokyo native, Eriko Yamaguchi.
In the company’s inception, Eriko partnered with a local factory that had been creating sacks for grain and potatoes out of coarse jute fabric, and began teaching workers how to create bags that could be sold for hundreds of dollars.
Living wages and a safe work environment have resulted in an average productivity rate that is 20% higher than other leather good factories. Eriko also gave her employees ID badges, a typical part of business culture in the West, but a gesture in Dhaka which gave workers a strong sense of pride in being valued by their employer.
After the horrible tragedy that unfolded at a Dhaka garment factory recently, I reached out to Eriko to try to understand what her company was doing to ensure the physical and mental safety of her employees. Here is our conversation (lightly edited):
John Gerzema: We are wondering what sorts of safety regulations you have put into your factory to assure nothing like this [the Rana Plaza collapse] ever happens?
Eriko Yamaguchi: In Bangladesh especially, in Dhaka and Chittagong cities, the factories are in congested spaces; in many cases factories were established in old buildings which were mainly constructed for commercial purposes not for factory purpose. Besides, due to space shortage many factories were working in multi-storied buildings with heavy machinery in high risk situations.
So, considering the above circumstances:
First, we have relocated our factory outside of Dhaka at Heymayetpur Industrial Area, which is very close to the proposed Tanney EPZ area. Though our factory building is under lease contract, but due to our relationship with the land owner, we have very closely monitored the construction work of the building and have cross checked the construction related soil-test result, building design, construction materials etc., with our design and construction consultant and got their approval on the factory building.
Second, our factory is very spacious with 25% free space added to the operating spaces; as a result our workers work in a flexible work environment with enough movement space.
Third, our factory is located on the ground floor. The factory is well equipped with fire fighting equipment (e.g. extinguishers, water supply, sand buckets). We have fire license issued by the Fire Department of Govt. after very strict inspection by the fire department. The license is regularly renewed. We also do fire evacuation/fighting drill regularly in every 3 months in the factory; we have a fire fighting team with 12 members who have gotten special training. Our factory has enough emergency exits and have an advantage of being open from three sides.
Fourth, no heavy machinery is installed inside the factory and our generator is installed outside of the factory in a safe space.
Fifth, our electric wiring system is regularly inspected inside the factory and maintenance is done every month to avoid fire accidents.
Finally, we also continuously discuss about safety system and make our workers aware about safety in the weekly general meeting in the factory.
JG: How have better working conditions affected the output of Motherhouse workers and why have you chosen worker safety over (possibly) increased profits?
Eriko: From the inception of the company and factory we have believed that “A better work environment will help us to produce better quality product.” With our belief we have found that in a better and safe workplace, our workers can do their work with more concentration and without any stress; as a result the productivity rate of our workers are on an average 20% higher than any other leather goods factory in Bangladesh. Therefore, providing safe and better working condition increases the possibility of making profit over the long run instead of affecting it.
JG: Do you believe that by paying higher wages to Motherhouse workers, they feel fulfilled and therefore perform their tasks without concern for safety?
Eriko: In our factory, our wage rate is higher than the average wages other factories in the leather goods factories. We also pay higher wages than the Govt. declare minimum wages for new workers. Our belief is paying the rational and logical wages to workers will make them loyal to the company. We consider our workers as the company assets—we train them, nourish them and invest in them for preparing them as long term employees of the company. We teach our workers workmanship, attitude, organizational behavior, health and safety, and team work. So our workers perform their job in our factory with complete mental satisfaction.
JG: Have the higher wages made Motherhouse workers more socially aware of the struggles of their peers?
Eriko: Actually, in fact higher wages is not the only motivating factor to work here. The total working environment, company management practices and other fringe benefit packages have been really attractive to our workers and potential job seekers. As a result our workers and staffs have an upper hand social status among their community and peers. So our workers also discuss many things about our factory to their outside associates; this is also a very effective channel for us to find out and recruit new workers.
JG: Having seen this tragedy happen in Bangladesh, what sorts of changes to work places in Dhaka would you suggest?
Eriko: In the current context of Bangladesh’s factories, we have these suggestions:
1. Factory owners should change their business philosophy from short term profit making to sustainable business development.
2. All factories located in Dhaka city should be shifted to outside Dhaka industrial areas with bigger space and better working environment.
3. Factory owners should consider their workforce as company assets and nourish them accordingly, instead of simply rushing after short term profit making.
4. All production factory operation should be run with a collaboration of factory owner, buyers and workers representative considering each other’s interests in constructive manner.
5. Finally, for ensuring factory health and safety; every factory should be established in 100% compliant factory building approved by concerned authorities and everyone should take the responsibility of creating good working environment.