An engineer holds up what looks like a silver shotgun shell. The shiny metal reflects the immaculate white walls of Tesla’s Gigafactory rising out of the Nevada desert. The cylinder contains silicon, lithium, and electrolytes, and fits easily into the palm of one hand. It is the electric-car company’s entire future. Without this battery, the Model III won’t sell at prices that a large number of Americans can afford. The company’s energy storage business will be stolen away by Asian manufacturers.
Batteries are the single most expensive component of an electric vehicle, and Tesla has aggressively sought to bring this cost down. By 2013, the price of the battery in its Model S was already less than a quarter of the car’s $72,000 price tag. But today’s battery makers have not demonstrated they have the capacity or the willingness to deliver affordable batteries at the scale Tesla needs to roll out a more mass-market vehicle. And so it’s building the Gigafactory. “The cost of batteries is so critical in all this that it justifies [Tesla] having this control,”says David Keith, an MIT professor studying automotive technologies. “No one else is going to push as hard as they want to bring down the cost of batteries, and to push the market as fast as they need it to go.”
Along with its partners, Tesla is pouring more than $5 billion into the Gigafactory, which will eventually cover an area equal to about 100 football fields, one of the largest buildings in the world. The company teamed up with Panasonic to build a factory capable of churning out 35 GWh of cells per year by 2018, more than total global production a few years ago. Musk raised the stakes again in 2015 by accelerating the construction schedule by two years. The Model III has secured an unprecedented 373,000 deposits from prospective buyers of the $35,000 electric vehicle for delivery in late 2017.
Tesla concluded it would not be able to lower its costs enough by simply replicating one of Panasonic’s existing battery plants. It had to redesign it from the ground up. “Over time, the majority of our engineering effort is going into engineering the factory as a product itself,” said Tesla’s CEO Elon Musk in a conversation with reporters last week at the Gigafactory. “It’s the machine that builds the machine. If we take creative engineers and apply them to design the factory, they make five to ten times more headway than improving the product itself.”
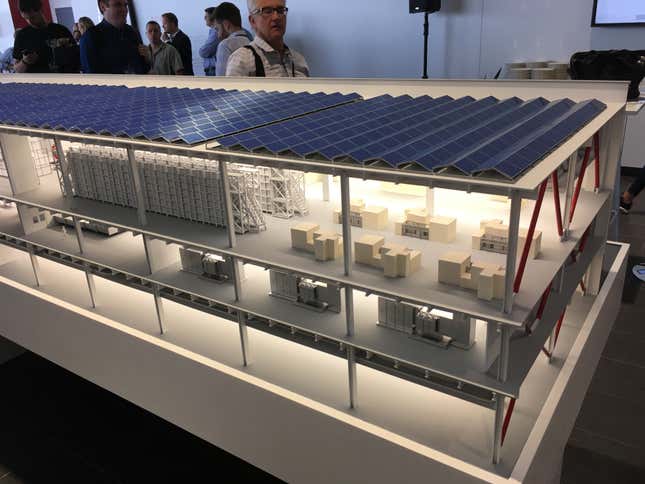
Strolling through the Gigafactory on a tour last week, a few things were evident. Despite being a construction site, very little appeared out of place, from steel beams neatly stacked in the dust to custom-designed safety signs. Most of the typical Silicon Valley perks had also been stripped away. Engineers and managers sat at long rows of white Ikea desks. Factory blueprints stamped “Tesla Confidential” filled up nearly every computer screen. There was no restaurant serving free food. Instead, a brushed aluminum buffet typical of public schools sat a few feet from the desks. Its chalkboard menu advertised veggie chili and cornbread for $7.
Batteries remain one of engineering’s most formidable challenges. Progress has been a frustrating series of stop-and-go breakthroughs followed by stagnation. Time and again, new discoveries have collided with manufacturing constraints and a still-incomplete understanding of battery physics, writes Quartz’s Steve LeVine in the book The Powerhouse, leaving a long line of defunct companies in its wake. Tesla, by contrast, says it has succeeded in making incremental changes by working with Panasonic to tweak engineering and manufacturing processes, and optimizing batteries for its car and storage applications. Since 2008, the cost of Tesla’s battery packs has been slashed in half and storage capacity has increased by around 60%.
The conversations in the Gigafactory returned to this same topic again and again: how Tesla will maximize efficiency to lower battery costs. Musk raised it during his afternoon interview, and his lieutenants repeated it on the factory floor. The Tesla team believes there are three variables it can control to build a cheaper battery that will outperform its competitors: materials, labor, and factory design. Every decision at the Gigafactory is intended to maximize at least one of them.
As a result, the Gigafactory is adopting some unconventional approaches. First, it’s being built as a series of mini facilities, each one iterating on the design of the last. Although the first phase of the Gigafactory is not yet complete, construction is already underway on the next (the factory’s exterior walls are removable). The first phase is more than double the capacity of a similar sized factory in Asia, said Yoshihiko Yamada, executive vice president of Panasonic, who was on-site working with Tesla’s engineers. Tesla plans to repeat this process numerous times. Today’s Gigafactory occupies just 14% of the planned area.
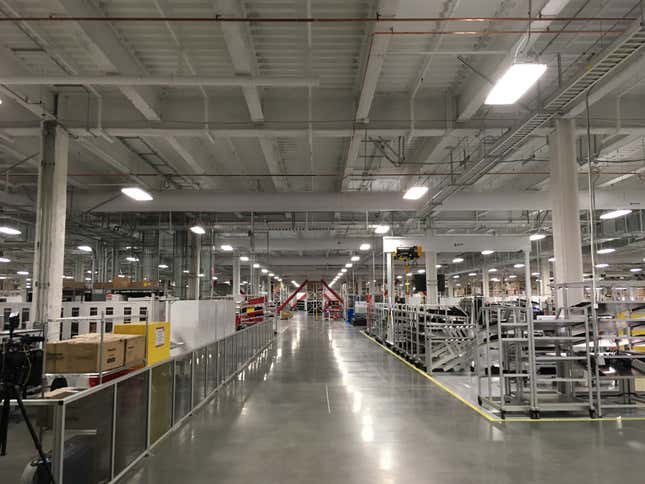
Tesla’s degree of vertical integration reverses a half century of US manufacturing strategy that has seen most of the supply chain leave the factory, often for overseas. At the Gigafactory, rail lines will ferry ore from Nevada’s lithium mines to the factory, and then ship out finished battery packs to Tesla’s car facility in Fremont, California. Panasonic says it has never worked so closely with any supplier to rethink its manufacturing process. “The two teams came up with ideas together,” said Yamada. “This type of relationship is quite new in business. It’s not really a simple buyer and supplier relationship.”
Finally, engineers are trying to recapture as much materials and energy costs as possible. The onsite waste, battery, and water recycling plants will reduce raw material demand. All fossil fuels were eliminated from the manufacturing process, unheard of for such a facility. Electricity will come from solar panels covering the factory roof, and on-premise batteries. Renewable power can be bought from the grid as needed, ensuring zero net greenhouse gas emissions.
While it builds out its factory, Tesla is racing against a global ramp-up in lithium-ion battery production. China’s BYD has poured billions into its own battery cell technology that will likely match Tesla’s battery production capacity by 2020, reports market research firm IDTechEx, while LG Chem of Korea, which supplies General Motors with battery packs for its Volt, expects to exceed this by manufacturing 50GW of cells by 2020.
This competition is already sending battery prices tumbling. The average lithium-ion battery pack has plunged to $150 per KWh from $1,200 per kilowatt hour in 2010, says MIT’s Keith. Musk predicted on Tuesday that the Gigafactory could reach $100 per KWh by 2020, beating industry projections by about five years. Although manufacturers’ battery prices are closely guarded secrets, Musk has said in the past that Tesla is ahead of curve: “We don’t think anyone is on a path to be even close to us.”
The Gigafactory approach is classic Musk. Set ambitious deadlines. Challenge the team to devise creative solutions. Press forward until the technical problems are solved (sometimes months or years after the initial target date). Repeat. So far, the strategy has largely worked. Tesla (and SpaceX) have delivered on most of Musk’s grand promises.
That strategy has its drawbacks. Tesla has lost five vice presidents this year, including the heads of of production and manufacturing, although Tesla has questioned the link to manufacturing pressures, Bloomberg reported. Its earlier Model S vehicles have sometimes fallen short of industry quality standards, according to Consumer Reports (Musk said these have been addressed). The company is also missing earlier production deadlines for the Model S, Model X, and Model 3 despite recent improvements.
The Gigafactory presents all these risks and more. Batteries are taking big steps forward after decades of incremental progress. Tesla risks investing in the wrong technology, and owning a very expensive mistake. “This is a risk on a risk,” writes IDTechEx of Tesla’s breakneck expansion. “[It’s] a massive volume ramp-up during a radical change of what you make.”
For Musk, there are few options. The company has produced 50,658 vehicles in 2015, and it has declared it wants to manufacture 500,000 vehicles per year by 2018, two years ahead of schedule. That means many more batteries. It’s “a huge, huge challenge,” says Keith.
“Toyota and other companies have taken 50 years to learn how to to do it,” he said. Tesla’s “ability to deliver on that is a huge question to me. It’s not that I doubt they can do it, or try very hard, but we should not underestimate [the difficulty] of what they are doing. Things are going to get very real over next few years.”